News
Save weight, space and cost with a distributed BMS
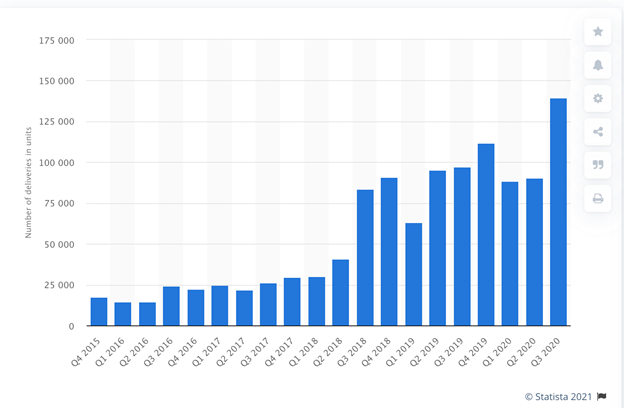
Figure 1 - Quarterly sales of a popular EV brand - source: Statista
By Philip Johnston, CEO
No amount of corporate planning by automotive executives could have predicted the outcomes experienced in 2020 due to the coronavirus. Disruption to supply chains, lockdowns, and concerns over job security have brought about what has been a torrid year for all the automotive brands. According to the Society of Motor Manufacturers and Traders, new UK car sales in 2020 plummeted to levels not seen since 1946. However, one ray of hope for the industry is that early indications point to a significant rise in the number of electric vehicles being sold.
Battery gigafactories become a topic of national interest
Automotive CEOs will welcome any sales growth to help their ailing balance sheets and validate the EV investment commitments they have already made. However, there is still much innovation required to deliver efficient battery technologies. There is also the drive to take the risk out of the supply chain by building national battery ‘gigafactories’ to maintain supply continuity. National and regional government initiatives have become ‘hot’ political agendas, such as the UK setting up a £1bn automotive transformation fund of which a gigafactory initiative is expected to take centre stage.
Achieving high levels of power density
From afar, the task of creating EV batteries might appear a simple one. After all, we already have one in our vehicle today, so scale it up a bit. Unfortunately, the power and voltage levels required to provide enough energy for sustained traction require batteries with a significant power density. Also, with physical space at a premium, the battery packs must be as small as possible. For example, the 85 kW Tesla S battery pack comprises 16 modules, each with 404 cylindrical 18650 cells. The interconnect between multiple modules creates a battery pack.
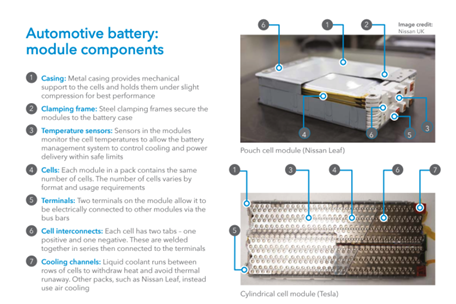
Figure 2: Extract from Automotive Batteries 101 by Professor David Greenwood, Advanced Propulsion Systems, (WMG, University of Warwick)
Batteries have specific chemistries that might vary slightly from cell to cell. Getting the most out of each cell and, consequently, the whole pack or module requires detailed monitoring using a battery management system (BMS) that continually checks parameters such as state of charge, state of health, state of function, temperature, and voltage. Load balancing takes account of individual cell efficiency operating on a pack and module basis. Safety features need to be incorporated too that allow individual cells to be taken out of the circuit should they exhibit signs of failure or poor performance.
Cell, module, and pack interconnect challenges
Squeezing the cells, the associated BMS sensors on each cell, and wiring them all together present several challenges. Firstly, there are the practical aspects of wiring together hundreds of cells in a time-efficient manner. Also, the mechanism used must safely insulate cell terminals from each other and the surrounding enclosure. Secondly, battery isolation and monitoring sensors need to be placed close to each cell. The sensor outputs can be fed to a central BMS; however, this involves more connectivity between cells, modules and packs. An approach gathering broad adoption is that of a distributed BMS, where each sensor and monitoring components and the associated control logic is contained local to the cells. This method, however, places constraints on the automated production techniques used to connect cells.

Figure 3: Improved Harness Technology™ enables flexi circuits to connect together individual cells to form battery modules in an electric vehicle
A viable solution to cell interconnect
An interconnect approach that satisfies the space and weight requirements while also enabling a distributed BMS method is using length-unlimited flexible circuits such as those Trackwise manufactures using its Improved Harness Technology™ (IHT). Figure 3 below illustrates the use of Trackwise IHT flexi circuits to connect together individual cells to form battery modules. Cell voltage, current, and temperature measurement components can be mounted on the flexi circuit in close proximity to the termination. Safety features, including cell isolation can also be incorporated using this approach. At the battery pack level, similar techniques can be utilized to place module monitoring, isolation and cooling control components.