News
Domestic EV battery manufacturing: securing the automotive industry’s future post-Brexit
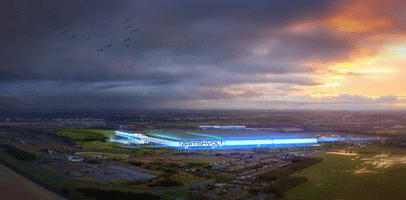
Photo courtesy of Britishvolt
By Philip Johnston, CEO;
While the first implications of Brexit are already felt across the UK industries, the real impact is yet to come. In six years’ time, the rules of origin will come into effect: to qualify for zero tariffs, a certain percentage of a component must be manufactured either in Britain or the EU. This is likely to be a challenge for the British EV industry. EV batteries, the single most expensive component in the vehicles, are traditionally made in Asia, making them subject to new taxes. As Europe is the biggest market for British-made vehicles, the UK automotive industry has to find new ways to ensure continued profitability when trading with the EU.
The obvious answer to the problem would be to manufacture the EV batteries in the UK. However, with most manufacturers currently relying on exports, the production is not yet established in the UK at the scale needed. According to some industry experts, the development has been slow compared to many Asian countries, such as China, Korea, and Japan, that invest heavily in EV battery technology. Even in Europe, many investment initiatives are already underway. Dr Andy Palmer, ex-CEO of Aston Martin, discussed the challenges in recent interviews with the BBC and Sky News, suggesting that the UK lags in investment. According to him, local EV battery production plants, or ‘gigafactories’, are crucial if the UK industry wants to benefit from the trend towards all-electric vehicles. As EV batteries are heavy and expensive, bringing battery production closer to the automotive manufacturing facility is key to improving profitability and safeguarding the industry against competition from Europe.
Des Quinn, the national officer for the automotive industries at the trade union Unite, also sees local manufacturing and ‘gigaplants’ essential for the industry’s survival. According to Quinn, EV manufacturers are more likely to move production to Europe than transport batteries to the UK.
In addition to the benefits to the industry, manufacturing EV batteries in the UK helps shorten the supply chain significantly as batteries no longer need to be transported over long distances. A greener supply chain helps manufacturers ensure that EVs live up to the public perception of them as sustainable cars.
Fortunately, some progress has already been made. Britishvolt is due to begin construction of its first gigaplant in Blyth, Northumberland, this year, with the plant fully operational by 2023. The £2.6bn investment is one of the most significant industrial events in the North East since Nissan opened a manufacturing facility in Sunderland nearly 40 years ago. Once the plant has been finalised in 2027, it is expected to employ up to 3,000 people, delivering over 300,000 lithium-ion batteries to the UK automotive sector each year.
Protecting a valuable industry
Developments like this that bring EV battery production closer to British manufacturers are vital for safeguarding the UK automotive industry. The sector generates billions of pounds in income and exports each year, employing hundreds of thousands of people. Investing in the British manufacturing ecosystem will not only protect jobs but also foster the development and deployment of new technologies. When EV batteries are manufactured locally, they can be better customised to meet car manufacturers’ needs in the UK and Europe while making the supply chain more sustainable. This is key to helping the UK meet its goal of zero net carbon emissions by 2050.
Some forward-thinking car makers have already taken steps to address the changes brought on by the new trade rules following Brexit. Nissan, for example, is moving the production of its higher energy batteries over from the US to its battery factory in Sunderland. Now owned by AESC Envision, the factory, which is currently manufacturing battery cells for the 40kWh packs used in Nissan’s Leaf models, will take on the production of 62kWh batteries used in Nissans’ Leaf e+.
Scaling up local production is also on the agenda for cell manufacturer AMTE Power. Facing increasing demand, the company plans to leverage lean and flexible manufacturing principles to develop its plant in Thurso, Scotland, to rival the production methods of gigaplants. By ramping up production, it hopes to provide better accessibility for the manufacturers of low volume specialist vehicles, who often lose out to large OEMs with higher volumes.
Shortening the supply chain for lithium
In order to produce EV batteries, manufacturers first need access to lithium. This has resulted in uncontrollable demand, posing a severe threat to the environment. What’s more, lithium has traditionally come from countries half a world away from the UK, such as Australia or China, adding to the strain. Even though some deposits have been discovered in Europe, the UK has not had a domestic source it could rely on. However, a recent discovery of a significant lithium deposit in Cornwall is likely to change this and revolutionise the UK supply chain. The operator, Cornish Lithium, has stated that it is committed to minimising the impact the mining activity has on the environment. Instead of using solar evaporation techniques that most operators rely on, it will use cutting-edge technology to extract the lithium from geothermal fluids. It claims the method to be more sustainable and efficient, saving a considerable amount of water and reducing the volume of waste generated.
Technologies such as this are further supported by research into other battery chemistries that reduce or fully eliminate lithium from the supply chain.
Modernising battery pack architecture
While the battery architecture has remained mostly unchanged for 40 years, a UK-based start-up Addionics is challenging this set-up. The company claims it can drastically improve battery performance by moving to a smart 3D architecture using a back-end manufacturing process. It says that the technology allows it to cut the charging time by half while doubling the range, with no impact on cost or reduction on lifetime. What’s more, the technology is compatible with any manufacturing process and can be integrated with any battery. This type of innovation, already on our doorstep, has great potential to contribute to a fully-functional domestic supply chain.
The structure of EV battery packs, including how the modules and cells are connected and monitored, is another aspect that needs consideration. High-voltage battery packs are traditionally difficult to build, and the process is time-consuming, regardless of if the components are connected in a series or parallel. There are two tabs in each cell: one positive, one negative. A module featuring a thermal interface and two connected terminals is formed by welding multiple cells together. The modules are then electrically connected with sensors and a controller to create a battery pack.
Unlocking new benefits with FPCs
For the battery packs to achieve optimal efficiency, they need to operate under carefully defined operating temperatures. To enable this, the cell’s temperature needs to be monitored at multiple points to protect it from overheating, optimise battery life and enhance safety. Alternatively, it is also possible to use flexible printed circuits (FPCs). The challenge is that, traditionally, FPCs are of limited length. Trackwise, however, is able to produce long flexi-circuits of virtually any length, using its Improved Harness Technology™ (IHT). It means that one circuit is able to connect all the cells into a module so that voltage, current, and temperature sensors are mounted on the FPC close to each cell. The technique also allows for additional safety features, including cell isolation, and enables the use of module monitoring, isolation, and cooling control devices at the battery pack level. The technology offers several advantages in terms of assembly and size. As it facilitates the use of automated production techniques, the assembly process is significantly quicker and easier. The battery pack’s size and weight are also reduced, thanks to the thinner and lighter flexi-circuits.
As these examples demonstrate, the future of British EV manufacturers looks much brighter than it did last year. The clock might be ticking, but the UK industry is well-prepared to meet the challenge of increasing battery production capacity over the next six years, edging it a step closer to becoming a world leader in EV production.
Photo courtesy of Britishvolt.